Green sand casting
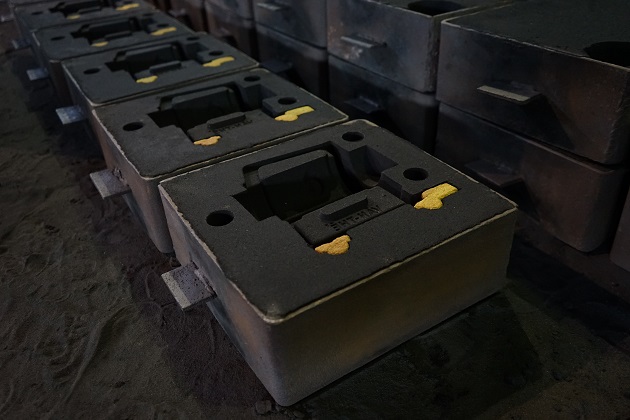
Green Sand Casting
Green sand casting is one of the most widely used and cost-effective metal casting processes. It involves creating molds using “green sand,” a mixture of sand, clay, water, and sometimes organic additives. Despite the name, “green” refers to the damp condition of the sand rather than its color. This process is versatile, economical, and suitable for producing a wide variety of metal parts in different sizes and shapes.
Key Features of Green Sand Casting:
- Cost Efficiency: The reusable nature of the sand and the simplicity of the process make it highly economical.
- Versatility: Applicable for casting a wide range of metals, including iron, steel, aluminum, and brass.
- Quick Production: The process is relatively fast and ideal for high-volume production runs.
- Good Surface Finish: Although the finish may not match that of precision casting, green sand casting provides acceptable surface quality for many applications.
Steps in the Green Sand Casting Process:
- Pattern Making: A model or pattern of the desired part is created using materials like wood, metal, or plastic.
- Mold Preparation: Green sand is packed tightly around the pattern in a mold box. The pattern is then removed, leaving a cavity in the shape of the part.
- Core Insertion (if needed): For parts with internal cavities, cores made from sand are placed in the mold.
- Pouring: Molten metal is poured into the mold cavity through a sprue or pouring system.
- Cooling: The metal solidifies as it cools inside the mold.
- Shakeout and Cleaning: The mold is broken, and the casting is removed. Excess sand is cleaned off the casting.
- Finishing: The casting may undergo additional processes, such as grinding, machining, or heat treatment, to achieve the desired specifications.
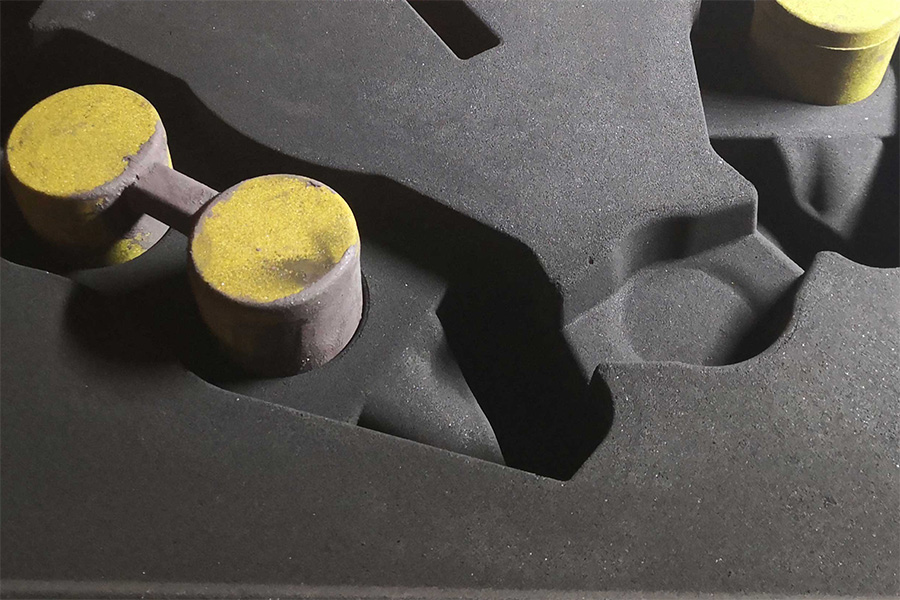