Investment casting
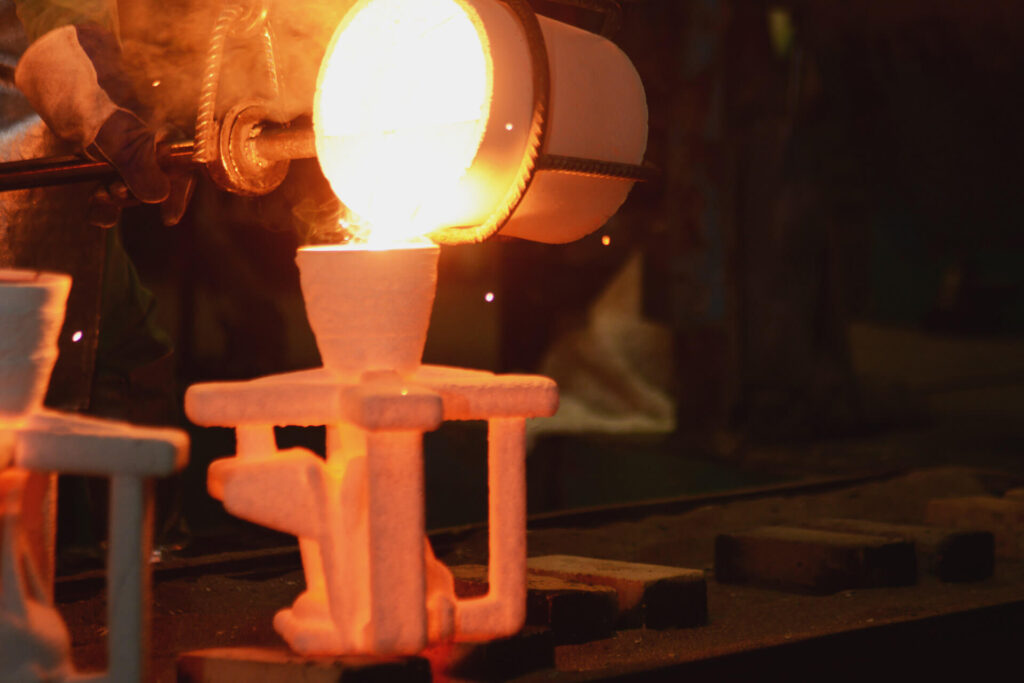
Investment Casting
Investment casting, also known as lost-wax casting, is a precision casting process used to produce complex and detailed metal components. This technique involves creating a wax model of the desired part, coating it with a ceramic material to form a mold, and then melting out the wax before pouring molten metal into the mold. Investment casting offers excellent dimensional accuracy, intricate detailing, and a high-quality surface finish, making it ideal for producing components with tight tolerances and complex geometries.
Key Features of Investment Casting:
- High Precision: Produces parts with tight dimensional tolerances and intricate designs.
- Excellent Surface Finish: Minimal need for secondary machining or finishing.
- Material Versatility: Can cast a wide range of metals, including stainless steel, aluminum, titanium, and superalloys.
- Design Flexibility: Supports thin walls, complex shapes, and fine details.
- Minimal Material Waste: Efficient use of material, reducing scrap.
The Investment Casting Process:
- Wax Pattern Creation:
- A wax model is made using a die or mold. For complex designs, multiple wax patterns may be assembled.
- Assembly of Wax Tree:
- Multiple wax patterns are attached to a central wax sprue to form a “tree,” allowing for the simultaneous casting of multiple parts.
- Ceramic Shell Formation:
- The wax tree is repeatedly dipped into a ceramic slurry and coated with fine sand to build a robust shell. Each layer is allowed to dry before applying the next.
- Dewaxing:
- The ceramic-coated wax assembly is heated to melt and remove the wax, leaving a hollow ceramic mold.
- Metal Pouring:
- The mold is preheated, and molten metal is poured into the cavity.
- Cooling and Solidification:
- The metal solidifies as it cools inside the mold.
- Shell Removal:
- The ceramic shell is broken away to retrieve the cast parts.
- Finishing:
- Excess metal is removed, and the casting undergoes machining, polishing, or heat treatment as needed.
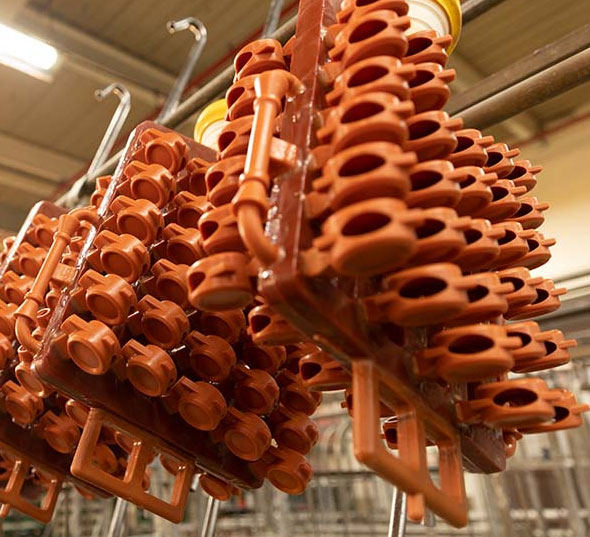