Lost foam casting
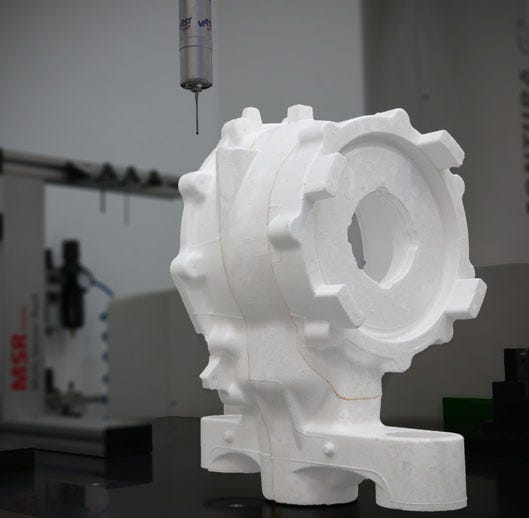
Lost Foam Casting
Lost foam casting (LFC) is an advanced casting method that uses an expendable foam pattern to create metal parts with high precision and minimal finishing. The process is ideal for producing complex shapes and achieving near-net-shape castings. The foam pattern is coated with a refractory material, surrounded by unbonded sand, and replaced by molten metal during pouring, which vaporizes the foam and fills the mold cavity.
Key Features of Lost Foam Casting
- Complexity: Capable of producing intricate geometries and integrated designs.
- Cost-Effectiveness: Eliminates the need for parting lines and cores, reducing machining and assembly.
- Surface Finish: Provides smooth and detailed surfaces.
- Material Versatility: Suitable for casting ferrous and non-ferrous metals, including aluminum, iron, and steel.
- Environmental Friendliness: Uses unbonded sand, which can be recycled.
The Lost Foam Casting Process
- Foam Pattern Creation:
- A foam pattern is made using expanded polystyrene (EPS) or similar materials, often formed by machining or molding.
- Pattern Assembly:
- Multiple foam patterns can be joined to create complex assemblies using adhesives.
- Coating:
- The foam pattern is coated with a refractory slurry to form a barrier that ensures smooth metal flow and prevents defects.
- Mold Preparation:
- The coated pattern is placed in a flask and surrounded with loose, unbonded sand, which is compacted to support the structure during casting.
- Metal Pouring:
- Molten metal is poured directly onto the foam, vaporizing it and filling the mold cavity with liquid metal.
- Cooling and Solidification:
- The metal cools and solidifies into the shape of the foam pattern.
- Shakeout and Cleaning:
- The sand is removed, and the casting is cleaned and finished as needed.
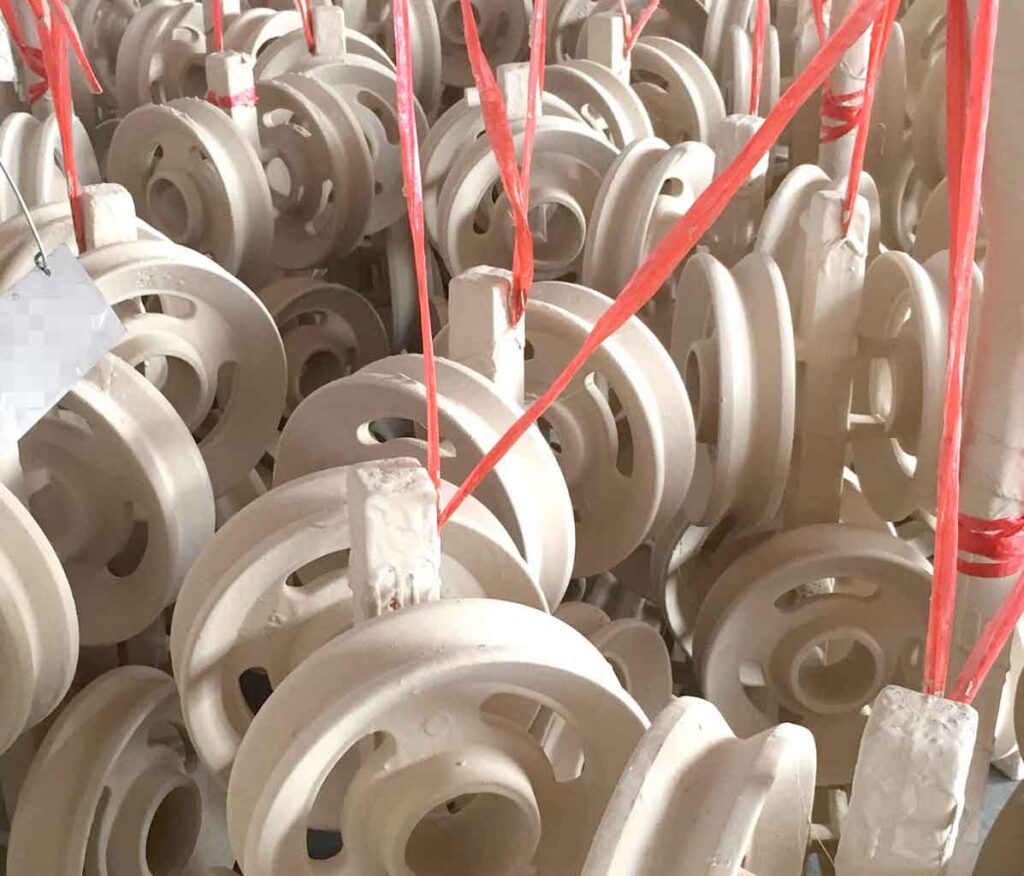